Optimizing Small Business Efficiency with 3D Printing
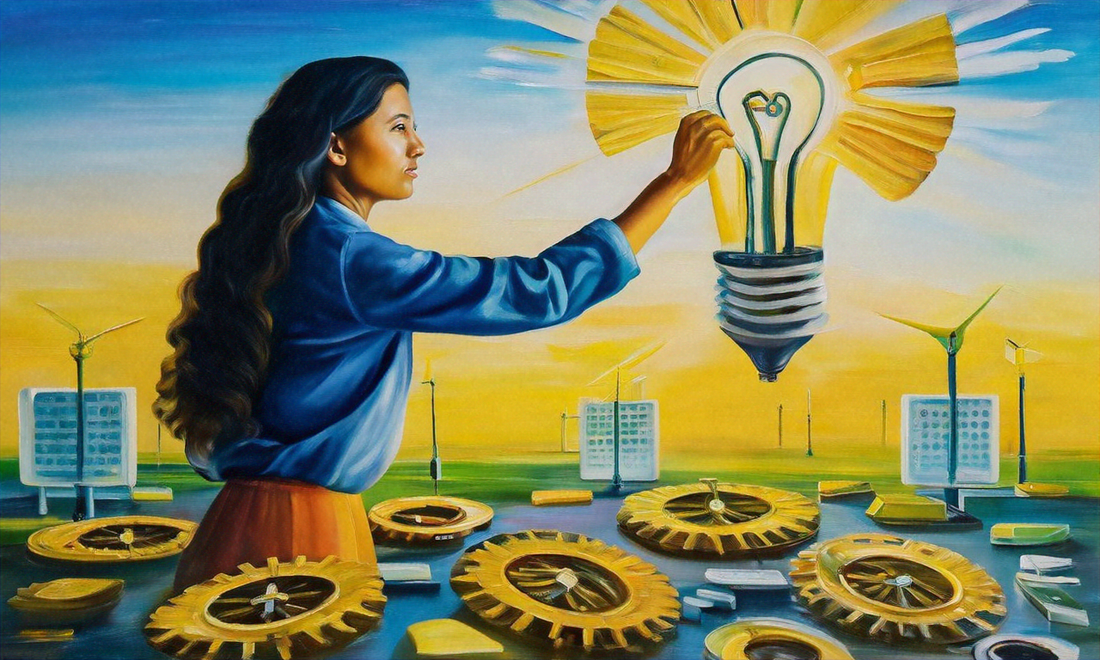
Integrating 3D printing into small business operations has become a game-changer in the realm of innovation and efficiency. Imagine being able to bring your product ideas to life rapidly, customize designs with ease, and optimize production processes seamlessly. In this blog post, we delve into the transformative potential of 3D printing technology for small businesses and explore how this integration can unlock new avenues for growth and competitiveness.
Benefits of Integrating 3D Printing into Small Business Operations
Cost Efficiency
Incorporating 3D printing technology can significantly reduce production costs for small businesses. By eliminating the need for traditional manufacturing processes and reducing material waste, businesses can achieve cost savings in the long run.
Time Savings
One of the key advantages of integrating 3D printing into small business operations is the ability to streamline prototyping and production processes. Rapid prototyping capabilities enable businesses to iterate designs quickly and bring products to market faster.
Customization Opportunities
Small businesses can capitalize on the customization possibilities offered by 3D printing. By leveraging this technology, businesses can tailor products to meet specific customer demands, leading to increased customer satisfaction and brand loyalty.
Key Points:
Cost efficiency through reduced production costs
Time savings due to rapid prototyping capabilities
Customization opportunities to meet unique customer demands
Overall, integrating 3D printing into small business operations brings about a range of benefits, including cost efficiency, time savings, and customization opportunities that can drive business growth and innovation.
Choosing the Right 3D Printer for Small Business Needs
Evaluating Printing Speed and Accuracy
When integrating 3D printing into small business operations, it's crucial to consider the printing speed and accuracy of the 3D printer. Different projects may require varying levels of precision and efficiency, so selecting a printer that aligns with the business's specific needs is essential.
Factors to Consider:
Printing speed: Evaluate the printer's speed capability to ensure efficient production timelines.
Printing accuracy: Assess the level of detail and precision the printer can achieve to meet quality standards.
Considering the Size and Material Compatibility
The size of the 3D printer and its compatibility with different printing materials are important factors to take into account. Small businesses with limited space may opt for more compact printers, while those requiring a wide range of material options should prioritize printers that support various materials.
Points to Note:
Printer size: Determine the physical dimensions of the printer to fit within the workspace efficiently.
Material compatibility: Verify the types of materials the printer can effectively work with for diverse printing needs.
Assessing Maintenance Requirements and Cost
Maintenance plays a significant role in the operational efficiency of a 3D printer. Understanding the maintenance needs and associated costs can help small businesses plan for ongoing upkeep and factor in maintenance expenses when budgeting for 3D printing operations.
Key Considerations:
Evaluate printing speed and accuracy for project suitability
Consider printer size and material compatibility for diverse printing needs
Assess maintenance requirements and associated costs for long-term operational planning
Selecting the right 3D printer tailored to the unique needs of a small business is a crucial step in optimizing efficiency and maximizing the benefits of integrating 3D printing into operations.
Implementing 3D Printing in Various Small Business Sectors
Manufacturing Sector
In the manufacturing industry, integrating 3D printing into small business operations can revolutionize rapid prototyping and product development processes. Businesses can leverage 3D printing technology to quickly iterate designs, test product concepts, and accelerate the overall production timeline.
Impact Areas:
Rapid prototyping: Shortening the prototyping phase to bring products to market faster.
Product development: Facilitating the creation of innovative and customized products with efficiency.
Retail Sector
Small businesses in the retail sector can enhance their offerings by incorporating 3D printing technology. Customization is a key advantage, allowing businesses to create unique products tailored to individual customer preferences. From personalized accessories to bespoke designs, 3D printing opens up a world of possibilities for retail businesses.
Benefits Include:
Customization opportunities: Meeting customer demands with personalized products.
Design flexibility: Adapting and iterating designs based on market trends and feedback.
Healthcare Sector
In the healthcare industry, 3D printing presents significant opportunities for small businesses to innovate and improve patient care. From creating customized medical devices to producing anatomical models for surgical planning, 3D printing technology can enhance the quality of healthcare services and address specific patient needs effectively.
Applications in Healthcare:
Personalized medical devices: Tailoring solutions to individual patient requirements.
Surgical planning tools: Enhancing surgical outcomes through detailed anatomical models.
Integrating 3D printing into various small business sectors like manufacturing, retail, and healthcare can yield remarkable benefits, enabling businesses to innovate, customize, and deliver high-quality products and services to their customers.
Overcoming Challenges and Pitfalls in 3D Printing Integration
Initial Investment and Budget Considerations
One of the primary challenges small businesses face when integrating 3D printing into their operations is the initial investment required. Purchasing 3D printers, materials, and software can entail a significant upfront cost. It's essential for businesses to carefully assess their budget and financial capacity before committing to 3D printing technology.
Key Points to Address:
Budget planning: Allocating funds for equipment acquisition and setup.
Return on investment: Evaluating the long-term benefits versus initial costs.
Staff Training and Skills Development
Another hurdle in 3D printing integration is ensuring that employees possess the necessary skills and expertise to operate and maintain the technology effectively. Providing comprehensive training programs and upskilling opportunities for staff members is crucial to maximizing the potential of 3D printing within the business.
Areas for Skill Development:
Operation of 3D printers: Training employees on the setup and operation procedures.
Design software proficiency: Enhancing skills in CAD modeling and design software usage.
Quality Control and Consistency in Printing Results
Maintaining consistent quality standards in 3D printing output is vital for small businesses to uphold their reputation and customer satisfaction levels. Factors such as print accuracy, material quality, and post-processing techniques must be monitored closely to ensure that the final products meet the desired specifications.
Ensuring Quality Assurance:
Regular calibration and maintenance checks: Preventing deviations in print quality.
Material selection and testing: Verifying the performance of different printing materials.
Addressing the challenges of initial investment, staff training, and quality control is essential for small businesses looking to successfully integrate 3D printing into their operations. By overcoming these hurdles, businesses can harness the full potential of 3D printing technology and enhance their competitive edge in the market.
Future Trends and Innovations in 3D Printing for Small Businesses
Advancements in Materials for Enhanced Functionality
The continuous development of 3D printing materials brings forth exciting opportunities for small businesses. Innovations in materials such as carbon fiber composites, flexible filaments, and metal powders expand the range of applications and capabilities of 3D printing technology. By leveraging advanced materials, businesses can create durable, high-performance parts and prototypes.
Key Material Innovations:
Carbon fiber composites: Introducing strength and lightweight properties to printed objects.
Flexible filaments: Enabling the production of bendable and resilient parts.
Metal powders: Facilitating metal 3D printing for robust and metal-grade components.
Integration with IoT and Automation Processes
The integration of 3D printing with Internet of Things (IoT) technologies and automation processes presents a new frontier for small businesses. By combining 3D printing with IoT sensors and data analytics, businesses can optimize production workflows, monitor print quality in real-time, and enhance operational efficiency. Automation further streamlines the manufacturing process, reducing manual intervention and enhancing productivity.
IoT and Automation Benefits:
Real-time monitoring: Tracking print progress and quality remotely.
Automated workflows: Increasing production speed and reducing labor costs.
Collaborative Opportunities in Additive Manufacturing Industry
Small businesses can tap into collaborative initiatives and partnerships within the additive manufacturing industry to foster innovation and growth. Collaborating with 3D printer manufacturers, material suppliers, or service bureaus can provide access to cutting-edge technology, expertise, and resources that may not be feasible to develop in-house. By engaging in collaborative projects, businesses can stay at the forefront of 3D printing advancements and expand their capabilities.
Collaborative Ventures:
Partnering with 3D printer manufacturers: Accessing the latest printer models and technologies.
Collaborating with material suppliers: Exploring new material options for diverse applications.
Embracing the future trends and innovations in 3D printing offers small businesses a competitive edge, enabling them to leverage advanced materials, integrate with IoT, automation, and explore collaborative opportunities to drive success and innovation in their operations.
Frequently Asked Questions About Integrating 3D Printing into Small Business Operations
How can 3D printing enhance product development for small businesses?
Integrating 3D printing enables small businesses to expedite prototyping, iterate designs quickly, and test concepts before full-scale production. This streamlined process accelerates product development timelines and fosters innovation.
What considerations should small businesses keep in mind when choosing a 3D printer?
Small businesses should evaluate factors such as printing speed, accuracy, size, material compatibility, and maintenance requirements when selecting a 3D printer. Understanding specific business needs and long-term goals is essential for making an informed decision.
Is staff training necessary for utilizing 3D printing technology in small businesses?
Yes, providing staff with training on operating 3D printers, CAD software, and maintenance procedures is crucial for successful integration. Skill development ensures efficient use of the technology and maximizes its potential within the business.
How can small businesses overcome the initial investment barrier associated with 3D printing?
Small businesses can explore financing options, leasing agreements, or cost-sharing programs to mitigate the upfront costs of acquiring 3D printing equipment. Calculating the long-term benefits and return on investment can also justify the initial expense.
What role does quality control play in 3D printing integration for small businesses?
Maintaining quality control measures is vital to ensure consistent and high-quality output in 3D printing. Regular calibration, material testing, and adherence to standards help small businesses deliver reliable products to customers and uphold their reputation.